The conversion of the
motion is probably a domain as important as its generation...
If one looks at the history of the volumetric motors,
which use pressurized gases rather than kinetic gases,
very few are the engines which take care about
about this aspect. For
example, the engine with pistons, rods and crankshaft , possesses a
kinematics, that in
addition to be very unbalanced, immediately imposes a frozen law of
conversion : even while making vary the radius of the crankshaft or the
lentgh of
the rods, the kinematics of the TDC/BDC is deplorable (too much long
and
stationary). One could mention other examples, as the Wankel where the
evolution of the volume of the combustion rooms, according to the angle
of rotation
of the output shaft, is not controllable, because of an
epitrochoïdal geometry that imposes all as soon as the
triangular geometry of the rotor is chosen.
Most of the engines
currently known aren't able to arbitrary impose
an evolution
of the volume of every room
according
to the angle of rotation of continually
rotating shaft of the motor.
And yet, at a time
where one tries
to
pilot the auto-ignition of gases by the rise of temperature during
the compression (with new field of research like the controlled
auto-ignition (CAI), high charge compression ignition (HCCI), active
thermo atmosphere (ATAC), and even piloted detonation...), very few
concepts worry about that and bring breaktough about the subject.
Only some inventors in Quebec noticed the advantage of a sudden and
intense TDC
to synchronize the auto-ignition of fresh gases very exactly with the
TDC, so that, in
a first time, the combustion is the most complete and clean, and in a
second time, the relaxation of gases occurs as early as possible to
push appropriately the mobile parts of their machine...
However it would be necessary to
be capable to generate the volume that one WANTS in EVERY ROOM
according to the angle
of rotation of the rotating shaft of the engine.
In the case of the SYCOMOREEN's rotary
pistons engines, it needs to
CONTROL the BEATINGS of the pistons... more precisely :
- their angular amplitude
- their minimal and
maximal angles of alternative rotation
- but also and especially the law of evolution of the beating
during a cycle "mini angle - > maxi angle - >
mini angle"
1.
Motion to convert
The POGDC engines are based on an octogonal piston with its heads which periodically move away and come closer.
2.
Proposed system
It is possible to use a standard system to convert the motion, by order of increasing relevance :
- rod /crank mechanism
-
sinus mechanisme
-
mechanisms with rotary cam(s) overmultilobed or not.
3.
Advantages of the mechanism with rotary multilobed cams
The
present mechanism based on a central rotative cam offers very numerous
assets :
- As regards to the transmission of
the efforts, pebble / cam or pebble / groove contacts are
very robust. And it's better when there are many pebbles, the power transits trough
several symmetrical paths inside the machine, what
guarantees a better reliability and a lighter sizing of the parts..
- When there is at least 2 lobs on each cam, the mechanism is perfectly and
intrinsically balanced because the effects of inertia of
the parts compensate themselves mutually.
- The rotative central cam has a 2 Pi / p cyclic profile, it is therefore well balanced
- The
shape of the
cam reflects the kinematics chosen for the angular law of rotation
coupling the rotary pistons with the central rotative cam. The
shape of the cam can be computed with any law from the moment it
doesn't generate collisions between the parts of the octogonal deformable piston and/or the carter.
- The interior envelope of the cam
doesn't present a quick angle in order to assure a better
guidance.
- The
choice of an interior profiled cam encourages the compactness of the
engine.therefore
4.
Examples of rotary central cam systems for not rotary POGDC engine
The
following pictures show the extreme
adaptability of the rotary cams design for all type
of not rotary POGDC engines.
POGDC with a 14 lobes central rotary cam

POGDC with a 6 lobes central rotary cam
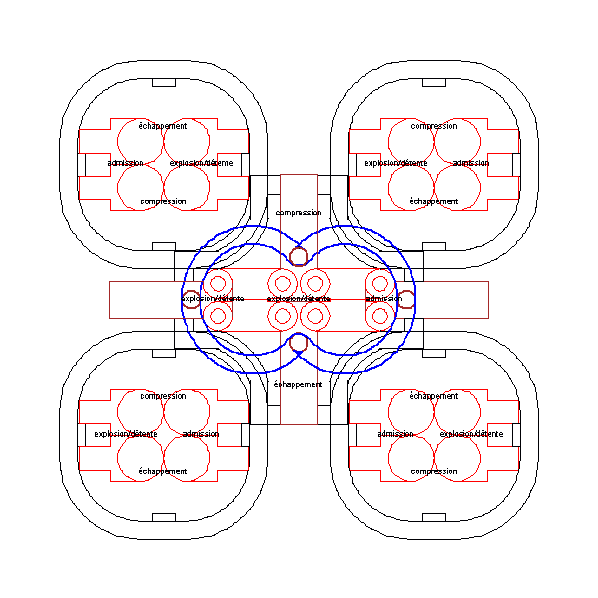
4
MPRBC + 1 POGDC with a 2 lobes rotary central cam

4
MPRBC + 1 POGDC with a 6 lobes rotary central cam
1
POGDC + 4 MPRBC with 4 monolobed cams

1
POGDC + 4 MPRBC with 4 hexalobed cams

1
POGDC + 4 MPRBC with 4 heptalobed cams

1 POGDC + 4 MPRBC with 2 counter-rotary bilobed cams
5. Examples of mechanism based on cams for rotary POGDC engines
6.
Over multi-lobed rotary central (2Pi /kp) cyclic cam
The rotary central cam can be over multi-lobed, by
machining
k . p lobes on the cam where k is positive integer superior
or equal to 2.
Why to over multi-lobe
the rotary central cam ?
it multiplies by k
the numbers necessary cycles
to 1 have one revolution of the cam...
therefore it
multiplies by k
the nominal compactness of the motor !
1.
The cam, in addition to convert the motion, plays a complementary role
of reducing gearings by a
k factor
2. The use of pebbles mounted on ball-bearings converts the power with
an output rate of about 95%
(contrary
to the successive trains of gearings whose output falls quickly unless
90% by rubbings / barbotages in oil)
3. All this functionalities are achieved by a single part with a
thickness of some millimiters
(laser
cuttable or usinable... in a simple plate of steel)
Under the condition to respect transmission angles which lead to
acceptable
efforts wether the engine works as a motor or a pump, and to give
sufficient size to the rotary central cam,
k can easily pass 3 or 4, in
particular for engines having few pairs of rotary pistons.
The following animation
belows show the extreme
variety of possible and arbitrary motions with over multi-lobed cams for
all type of POGDC engines.